Quality has always been a crucial factor in manufacturing, but today quality management is more important than ever as customers have more choices and easier access to information about competing products. Manufacturers have access to tools for building quality and efficiency into their processes, such as manufacturing execution systems software solutions (MES), warehouse management systems (WMS) and quality management systems (QMS). While each of these systems provides visibility, tracking and insights that fuel greater quality control and management, implementation of several disparate tools can lead to production delays and difficulties — defeating the purpose of the individual solutions.
Lack of cohesion threatens efficiency and quality
Disparate solutions provide value in various areas of your supply chain, but they can also introduce nonconformity to processes. For example, when incorporating corrective and preventative actions into the manufacturing process, systems that do not connect and orchestrate together lead to inconsistencies. The complex nature of modern manufacturing requires systems that mesh together, providing seamless continuity of efficiency, quality management, control and continuous improvement for future growth.
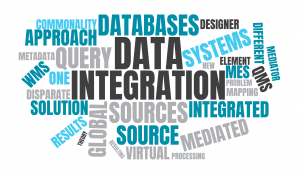
Issues with disparate systems
Without integrated systems for supply chain and quality management, manufacturers face possible production delays from the need to manually enter data or maintain a separate tracking system, such as paper or spreadsheet data collection. These delays spread, adding turnaround time to inspections and QC sampling. Disconnect between manufacturing and warehousing and logistics further exacerbates quality concerns, leading to waste and further delays.
Lack of integration leads to a domino effect, resulting in a need to carry more inventory on hand to compensate for quality control deficiencies and added expense and wasting of valuable warehousing and product resources.
More crucially, however, disparate systems work against overall organizational efficiencies. Different software solutions lead to siloed departments and an “us against them” mentality between production, quality control and logistics. While this situation is less than optimal for organizational efficiency, it also results in QC approval of unapproved products, manual efforts in report testing that are inefficient and less accurate, and hinder moves to paperless manufacturing — a primary goal of MES software solutions. Paperless manufacturing centralizes all information associated with production, supporting continuous improvement and lean manufacturing initiatives.
A closed-loop solution to integrate QM processes
Rather than relying on a handful of separate solutions — and worrying about the risks of disparate systems — manufacturers should move to a closed-loop, fully integrated solution for managing and tracking overall equipment effectiveness (OEE) and quality from gate to gate. Through integration, manufacturers can increase productivity and ensure greater levels of quality. Integration eliminates the problems associated with disparate systems, such as inaccurate or incomplete record-keeping and a lack of visibility from one department to another.
A closed-loop system contains information for improved accuracy and visibility for a holistic approach. With the ability to see accurate, real-time information at any stage of manufacturing or quality control, all corrective and preventative actions carry more meaning, as consistent application of these actions can be assured.
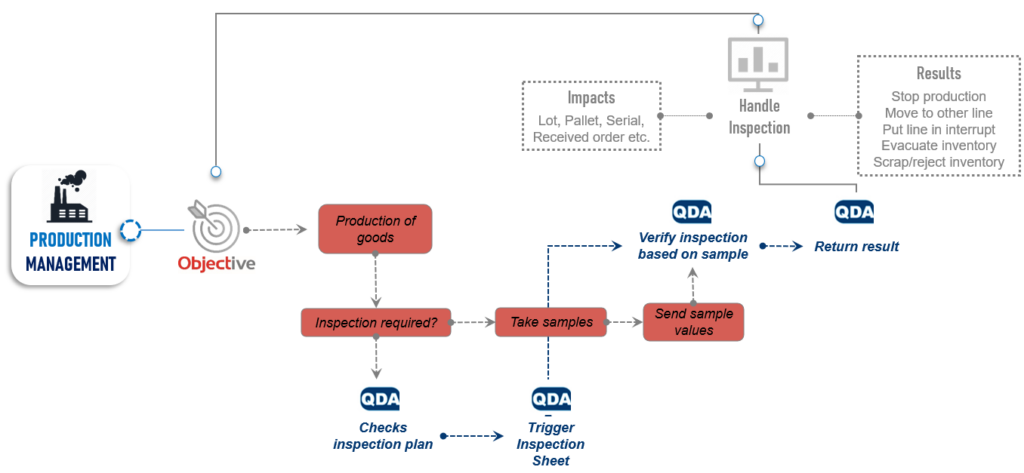
Drive consistent performance
QDA SOLUTIONS integrates with Objective MES, helping manufacturers maintain consistent and accurate control of their entire production, quality control, and logistics processes. The closed-loop system incorporates OEE, logistics/warehousing, data collection, laboratory information systems (LIMS), non-conformance management, integrated quality planning, supply chain management, and more. From reduced stock requirements to fewer logistic movements, manufacturers experience cost savings as well.
Beyond efficiencies, the solution aids in compliance, eases audit concerns and easily integrates with other systems, such as ERP solutions and PLC/SCADA machines. Through this integration, manufacturers can drive down costs and improve product quality.
The closed-loop system’s consistency also provides a single standardized configuration for multi-site operation and 24/7 system support. With Objective and QDA SOLUTIONS you can handle all quality needs from design and development to delivery and distribution and achieve a global view of all your company’s quality in one solution.
The result is seamless, accurate, and fully transparent production, so manufacturers know the status of their processes and can more accurately and effectively deliver results today and for the future. Manufacturers can meet their operational efficiency and quality management goals, because the expertise in all departments, from production to warehouse to quality control, can be fully leveraged.
For more information on how the solution’s integrated quality management systems can power efficiencies, drive performance, maintain market competitiveness, and improve customer experience, contact us for more information.