CUSTOMER FEEDBACK | Integration
Customer feedback has become an integral and important part of compliance requirements, and failure to manage it is the leading factor named in non‐compliance citations. Many manufacturing companies have complaints that evolve into non-conformances because they fail to analyze, follow through and get to the root cause concern. In addition, companies get into trouble because there is no tie-in to a corrective and preventive action or management review.
QUALITY DATA | Integration
QDA SOLUTIONS Non-Conformance Management solution tags a specific complaint to the product in question and pulls in all the quality data and history associated with it. This provides powerful analysis and traceability from the complaint back to its source so that the user gains valuable lessons learned before closing out an issue or project.
Complaints and other defined conditions, such as repetitive errors or at-risk products, may be set to automatically trigger corrective actions, define responsible parties and deadlines to complete the action. In turn, the software can trigger escalation mechanisms and reporting.
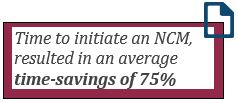
WORKFLOW | Integration
The process of integrating complaints is energized through workflow integration. Tasks are prioritized by severity or other predefined criteria and dispatched to individuals or teams in affected areas such as production, receiving and service. This streamlined approach allows key individuals to act decisively on top priority issues.
ERP – MES – QMS Systems | Integration
The QDA software is an integrated part of a quality management system (QMS), ERP and MES systems. This integration enables the use of the complaint management solution across all functions and capabilities of on enterprise software system. The system has a centralized database architecture that is fully inter-operable with industry standard databases. This allows you to build upon the strength of your existing platform and applications with minimal effort.
Data and information from the entire QMS can be integrated, from laboratory test data, auditing results and SPC control chart to incoming inspections and your supply chain.
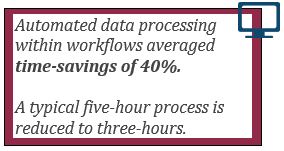
COST | Integration
You need a solution that can also capture costs associated with complaints and their processing, facilitating development of relevant financial analysis and management reports. Cost data can then be sent along to your ERP system.
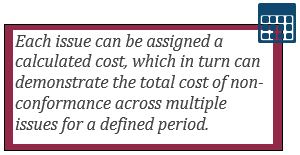
COMMUNICATION | Integration
Getting the right information to key individuals in a timely manner circumvents issues and can save significant costs from rework, scrap and warrantee claims. Simply determine user-defined parameters, and a complaint will be automatically routed for investigation, response, and reporting. Notifications can be sent to specific departments and personal automatically from email. And an escalation procedure can be triggered when a severity and priority threshold is reached.
REPORTING | Integration
The solution consolidates graphical and analytical input from complex data collection and analysis operations into easy to produce, meaningful report formats. Reports may be generated and developed using predefined or custom templates. The user may select from a number of predefined logical and intuitive report formats (including 8D and PPM).
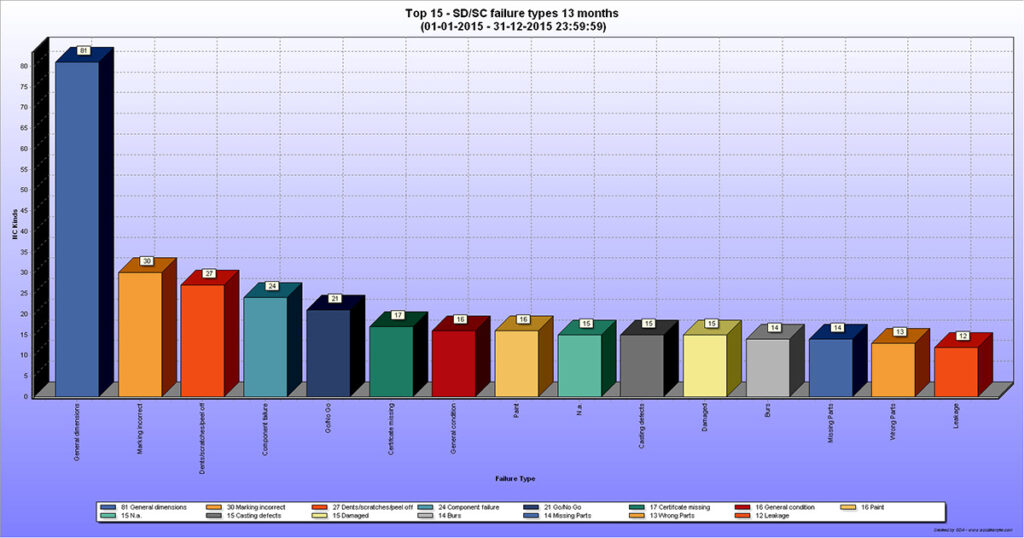
Gain visibility into the complaints database and lifecycle with comprehensive aggregate reporting as well as individual case status tracking. The system gives you the ability to associate various complaint types for spotting trends and common sources of non-conformances ensures timely preventative actions. Graphical executive dashboards provide statistics and data by a variety of complaint parameters, such as type, products, and status, due dates, closure times, plants, region and lots. Unique drill downs capabilities take the user to the finest level of detail to see the underlying data. The system provides quick access to graphical scorecards or tabular data that can be easily exported in industry standard formats and layouts.
CONTINOUS IMPROVEMENT | Integration
Relevant findings can quickly become an integral part of the process and bring clarity to the issues and drive root cause analysis and continuous improvement decisions. With the QDA SOLUTIONS Non-Conformance Management system you can keep complaints under control with automated workflows and integrated data from other relevant areas. The system brings in ISO Standards and FDA mandates, ties in CIP and CAPAs and consolidates finds into intuitive focused report and decisive actions.
Turn your customer complaints into continuous quality improvements with an automated and integrated system. Giving you the proactive visibility to root cause issues and clarity you need to make decisive change.
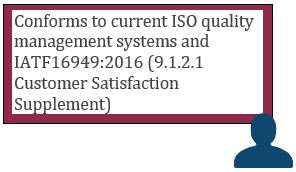