Doch woran genau liegt es, dass die Fehlermöglichkeits- und Einflussanalyse, so der volle Name der Methode, zwar in so ziemlich jedes QM-Handbuch Eingang gefunden hat, in der betrieblichen Praxis dann manchmal aber doch nur eine Nebenrolle spielt? Nun, wie so oft bei den wirklich guten QM-Methoden ist es auch bei den FMEAs so, dass sie allzu schnell Opfer ihres eigenen Erfolgs werden. Denn: Je wirkungsvoller potenzielle Fehlerquellen aufgespürt und mit passenden Gegenmaßnahmen so weit wie möglich geschlossen werden, desto seltener treten die mit den Risiken verbundenen Qualitätsmängel im Echtbetrieb noch auf. Vor diesem Hintergrund ist es elementar, präzise belegen zu können, wo in den Produkt- und Prozess-Designs man welche Defizite erkannt hat, welche Kritikalität diese Schwachstellen haben und welche Vorkehrungen getroffen werden, um die daraus resultierenden Risiken ausreichend abzustellen.
Nur über eine solche Erfolgsmessung lassen sich die Ressourcen sichern, die zur kontinuierlichen Fortführung eines FMEA-Programms zwingend erforderlich sind. Schließlich ist die Methode immer auch ein Kostenfaktor – und zwar insbesondere dann, wenn man es wirklich ernst meint und tatsächlich alle Stakeholder einbezieht, die in den zu untersuchenden Produkt- und Prozess-Designs eine wesentliche Rolle spielen. Typischerweise umfassen FMEA-Teams dann Konstrukteure, Analysten, Prozesssteuerungsingenieure, Fertigungstechniker, Kundendienstmitarbeiter und Manager. Hinzu kommen Produktteam-Mitglieder aus der operativen Wertschöpfung. So etwa aus der Vorserienfertigung. Mitarbeiter also, die die betreffenden Teile schon einmal verbaut haben und mögliche Qualitätsprobleme daher am besten kennen. Um all diese Stakeholder an einen gemeinsamen Tisch zu holen, ist es absolut essenziell, so belastbar wie möglich belegen zu können, welche Mehrwerte vergleichbare FMEA-Projekte bereits erzielt haben.
Vorhandenes Wissen nutzen
Die Rechtfertigung der Analyseaufwände ist jedoch keineswegs der einzige Faktor, der für die Durchführung von Erfolgsmessungen spricht. Schließlich liegt der Charme aussagekräftiger Ergebnisdokumentationen auch darin, dass diese als Referenzpunkt für alle vergleichbaren FMEA-Projekte dienen. Je umfassender man die bereits bekannten Qualitätsprobleme und die damit einhergehenden Vermeidungsmaßnahmen recherchieren kann, desto effektiver lassen sich Wiederholfehler in artverwandten Prozess- und Produkt-Designs ausschließen.
Dies erfordert die uneingeschränkte Wiederverwendbarkeit früherer Untersuchungsergebnisse. Eine Forderung, die inzwischen auch der Industriestandard AIAG & VDA FMEA stellt, der seit 2019 von beiden Verbänden gemeinsam herausgegeben wird und sich seitdem auch außerhalb der Automobilindustrie zur wichtigsten Leitlinie entwickelt hat, wenn es um den Aufbau eines funktionierenden FMEA-Regimes geht.
Der Standard gliedert sich auf in sieben Teilschritte. Diese sind:
- Strukturanalyse
- Planung und Vorbereitung (Scoping)
- Funktionsanalyse
- Fehleranalyse
- Risikoanalyse
- Optimierung
- Ergebnisdokumentation
QDA FMEA, die FMEA-Lösung unseres integrierten CAQ-Systems, folgt dieser Agenda. Die Anwender erhalten normenkonforme Templates und Workflows, um jeden dieser Teilschritte einheitlich auszuführen. Gleichzeitig ist sichergestellt, dass sämtliche FMEAs in einer zentralen Datenbank gespeichert werden, so dass alle Teams im Unternehmen in geordneter Form darauf zugreifen können.
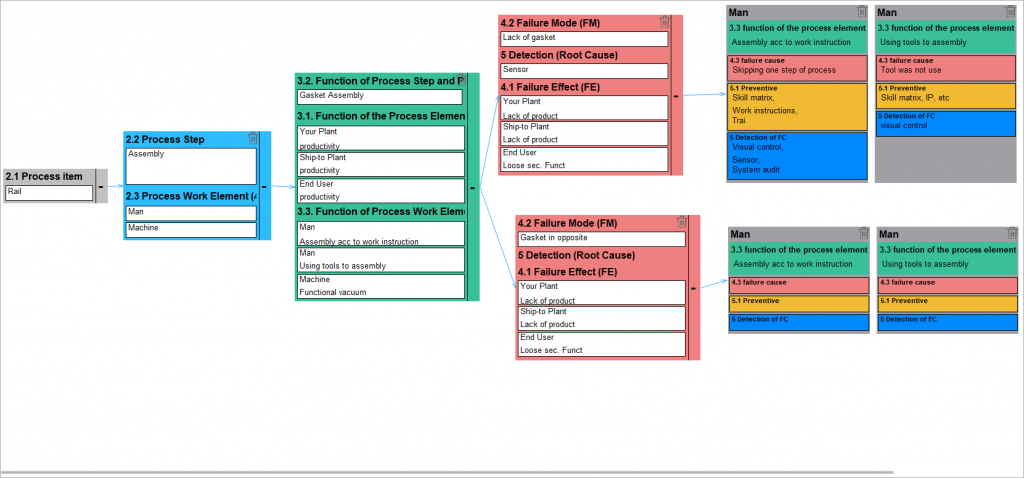
Die konsistente Erfassungs- und Verarbeitungs-Systematik fördert die Vergleichbarkeit der Analysen. Gleiches gilt für die Weiterverwendung der gewonnenen Erkenntnisse. So ist es beispielsweise möglich, das FMEA-Wissen in den darauf aufbauenden QM-Dokumenten weiterzuverarbeiten, ohne die Daten noch einmal neu erfassen zu müssen. Zu diesen Dokumenten zählen zum Beispiel Prozessablaufdiagramme, Produktionslenkungspläne oder auch Prüfpläne.
Change-Bedarf nicht unterschätzen
Rein systemtechnisch gesehen sind damit alle Voraussetzungen erfüllt, um FMEAs auch außerhalb der Automobilindustrie flächendeckend einzusetzen. Doch um die Methodik erfolgreich anwenden zu können, sind mancherorts noch Hausaufgaben zu erledigen. Um zu verstehen worin diese bestehen, lohnt sich ein Blick auf drei wichtige Erfolgsfaktoren, die gut funktionierende FMEA-Programme kennzeichnen.
Der erste dieser Faktoren klingt einfach, ist aber in der Praxis immer wieder eine echte Herausforderung. Die Rede ist vom richtigen Timing. Dieses zeigt sich vor allem darin, dass man so früh wie möglich mit der Analyse beginnt. Denn: FMEAs sollten nach Möglichkeit genau zeitgleich zu den Planungsprojekten starten, die Produktentwicklungen oder Prozessanpassungen zum Ziel haben. Nur so können die Analysen ihre volle Vorhersagekraft entfalten. Demgegenüber hat eine eher retrospektive Betrachtung immer den Nachteil, dass die daraus ableitbaren Maßnahmen der Realität permanent hinterherlaufen. Zudem besteht die Gefahr, dass solche Ex-post-Maßnahmen zu wesentlich höheren Umsetzungskosten führen, als dies bei einer Analyse der Fall ist, die parallel zum eigentlichen Entwicklungsprojekt erfolgt.
Hier ist Augenmaß gefragt. Vor allem zu Beginn von Engineering-Projekten, wo Qualitätsplanung nicht unbedingt das ist, wonach sich die Entwicklerteams gerade am Stärksten sehnen. Vor diesem Hintergrund sollte darauf geachtet werden, dass man den Fokus der Risikobetrachtung passend einstellt. Je genauer der Scope der Analyse dann gezogen wird, desto direkter erkennen sich die zu beteiligenden Stakeholder in der FMEA wieder und desto eher tragen sie auch aktiv zu deren Gelingen bei.
Den Finger wirklich in die Wunde(n) legen
In der Praxis ist das FMEA-Thema in der Entwicklung aufgehängt und wird von dort aus gesteuert. In vielen größeren Unternehmen gehen die Qualitätsplaner mit in die Verantwortung. Abgesehen davon ist es jedoch sinnvoll, die praktische Durchführung der Analyse in die Hände eines unabhängigen Dritten zu geben. Vorzugsweise sollte dies jemand sein, der mit dem eigentlichen Gegenstand der Analyse noch keinerlei Berührungspunkte hat. Wichtig ist zunächst einmal nur, dass er mit der Methode vertraut ist. Hieraus ergibt sich der zweite wichtige Erfolgsfaktor für wirklich aussagekräftige Analysen. Denn je weniger vorgefasste Annahmen der reine Methodenspezialist darüber mitbringt, wie der zu untersuchende Prozess in der Praxis laufen sollte, desto größer ist die Wahrscheinlichkeit, dass er auch genau die Fragen stellt, die wirklich weh tun.
Wer dagegen ein reines Insider-Team hat, läuft Gefahr, einige der relevantesten Risiken nicht kritisch genug zu hinterfragen. Denn nicht wenige Qualitätsdefizite haben Ursachen, die bei der Konzeption neuer Produkte und Prozesse als zu banal erscheinen, um ernsthaft thematisiert zu werden. Ein externer Moderator hat diese Voreingenommenheit nicht. Er kann daher alles in Frage stellen und versetzt das Team in die Lage, sich mit allen relevanten Risiken ernsthaft auseinanderzusetzen.
Niemals zurücklehnen
Im Prinzip ist eine Fehlermöglichkeits- und Einflussanalyse damit niemals fertig. FMEAs haben auch gar nicht den Anspruch, jemals abgeschlossen zu sein. Sie sind lebende Dokumente, die fortlaufend aktualisiert werden müssen. Mit frischen Erkenntnissen, die aus der Fertigung und Montage oder auch aus dem Feld kommen. All diese Rückmeldungen gilt es zeitnah zu bewerten, um die bisherigen Maßnahmen gegebenenfalls anzupassen oder zusätzliche Vorkehrungen zu treffen. Hier liegt der dritte zentrale Erfolgsfaktor.
Letztlich erfolgt die Weiterentwicklung der FMEAs dann so lange, wie die Produkt- und Prozesslebenszyklen andauern, für die die Analysen konzipiert sind. Unternehmen halten damit ein äußerst wirkungsvolles Instrument in den Händen, um die Potenziale der kontinuierlichen Prozessverbesserung nachhaltig zu erschließen.